Łączenie dwóch kompresorów to proces, który może przynieść wiele korzyści, zwłaszcza w kontekście zwiększenia wydajności i efektywności systemu pneumatycznego. W pierwszej kolejności warto zrozumieć, jakie są różne metody łączenia kompresorów. Najczęściej stosowane podejścia to połączenie równoległe oraz szeregowe. Połączenie równoległe polega na tym, że oba kompresory pracują jednocześnie, co pozwala na zwiększenie wydajności powietrza dostarczanego do systemu. Z kolei połączenie szeregowe oznacza, że jeden kompresor zasila drugi, co może być przydatne w sytuacjach, gdy potrzebna jest wyższa ciśnienie. Ważnym aspektem jest również dobór odpowiednich rur i złączek, które będą w stanie wytrzymać ciśnienie generowane przez oba urządzenia. Należy także zwrócić uwagę na to, aby kompresory były kompatybilne pod względem wydajności i ciśnienia roboczego.
Jakie są zalety łączenia dwóch kompresorów?
Łączenie dwóch kompresorów niesie ze sobą wiele korzyści, które mogą znacząco wpłynąć na efektywność pracy w różnych branżach. Przede wszystkim, dzięki takiemu rozwiązaniu można uzyskać większą wydajność powietrza, co jest szczególnie istotne w przypadku intensywnego użytkowania narzędzi pneumatycznych. Dodatkowo, połączenie dwóch kompresorów pozwala na lepsze zarządzanie obciążeniem, co może prowadzić do dłuższej żywotności urządzeń oraz mniejszych kosztów eksploatacji. W przypadku awarii jednego z kompresorów, drugi może przejąć jego funkcje, co zwiększa niezawodność całego systemu. Kolejną zaletą jest możliwość dostosowania ciśnienia do specyficznych potrzeb aplikacji poprzez regulację pracy poszczególnych urządzeń. Dzięki temu można uniknąć sytuacji, w której jedno z urządzeń pracuje na granicy swoich możliwości, co mogłoby prowadzić do uszkodzeń czy awarii.
Jakie są najważniejsze kroki przy łączeniu kompresorów?
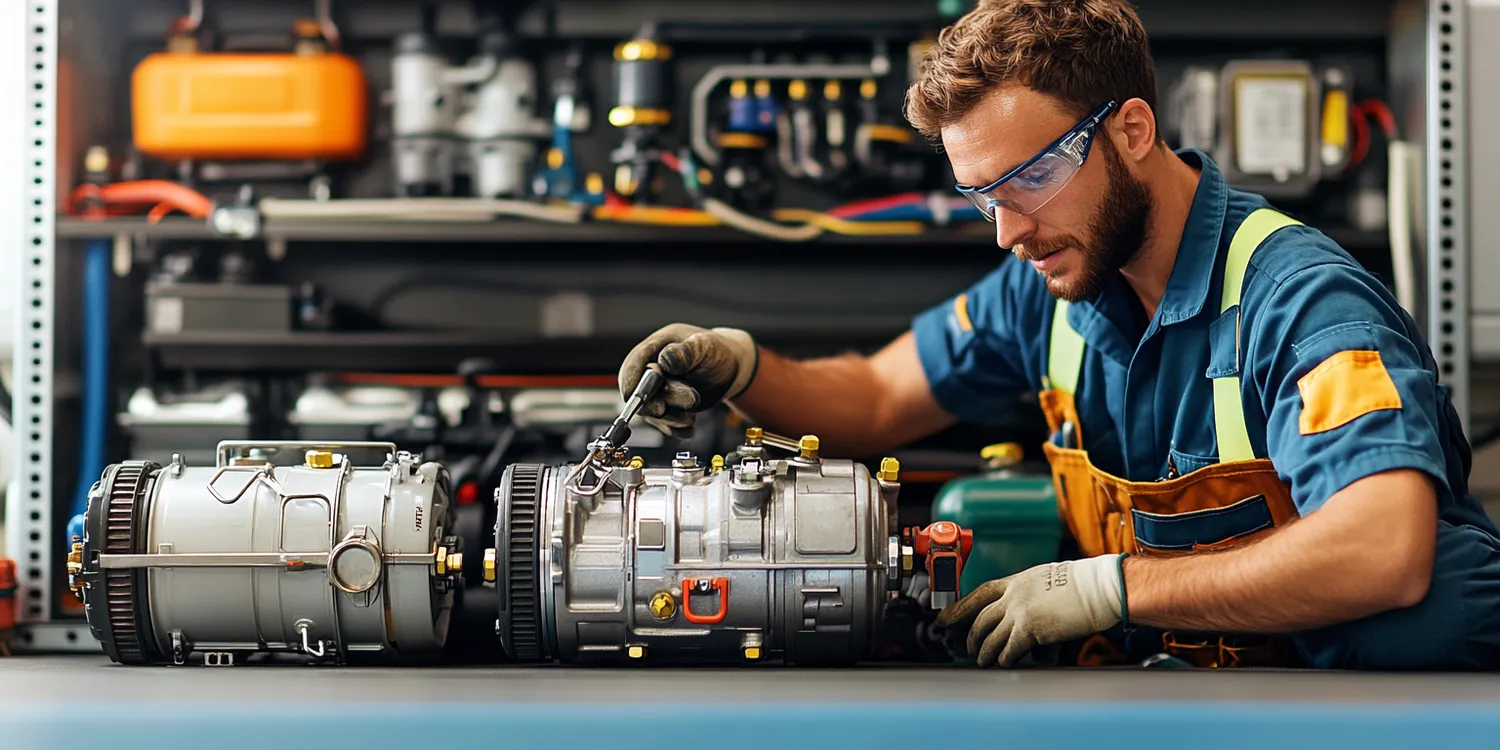
Proces łączenia dwóch kompresorów wymaga staranności oraz odpowiedniego planowania, aby zapewnić ich prawidłowe działanie i bezpieczeństwo użytkowników. Pierwszym krokiem jest dokładna analiza specyfikacji technicznych obu urządzeń oraz ich parametrów roboczych. Należy upewnić się, że oba kompresory mają podobne wartości ciśnienia i wydajności, aby uniknąć problemów z ich synchronizacją. Następnie warto zaplanować układ rur i złączek, które będą łączyć oba urządzenia. Kluczowe jest dobranie odpowiednich materiałów odpornych na wysokie ciśnienie oraz zapewnienie szczelności połączeń. Kolejnym krokiem jest instalacja zaworów bezpieczeństwa oraz manometrów kontrolnych, które pozwolą monitorować ciśnienie w systemie i zapobiegać ewentualnym awariom. Po zakończeniu montażu należy przeprowadzić testy działania całego układu, aby upewnić się, że oba kompresory współpracują ze sobą bezproblemowo.
Jakie są najczęstsze problemy przy łączeniu kompresorów?
Podczas łączenia dwóch kompresorów mogą wystąpić różnorodne problemy techniczne, które mogą wpłynąć na ich wydajność oraz bezpieczeństwo użytkowania. Jednym z najczęstszych problemów jest niewłaściwe dopasowanie parametrów roboczych obu urządzeń. Jeśli jeden z kompresorów ma znacznie wyższą wydajność lub ciśnienie niż drugi, może to prowadzić do przeciążenia słabszego urządzenia oraz jego szybszego zużycia lub awarii. Innym problemem może być nieszczelność połączeń rur i złączek, co prowadzi do utraty ciśnienia i obniżenia efektywności całego systemu. Ponadto niewłaściwe ustawienie zaworów regulacyjnych może skutkować nieoptymalnym działaniem kompresorów oraz ich nadmiernym zużyciem energii elektrycznej. Warto także zwrócić uwagę na hałas generowany przez dwa pracujące jednocześnie urządzenia; jeśli nie zostaną podjęte odpowiednie środki zaradcze, może to prowadzić do przekroczenia dopuszczalnych norm hałasu w miejscu pracy.
Jakie narzędzia są potrzebne do łączenia kompresorów?
Przy łączeniu dwóch kompresorów niezbędne jest posiadanie odpowiednich narzędzi i materiałów, które zapewnią prawidłowy montaż oraz późniejsze użytkowanie systemu. W pierwszej kolejności warto zaopatrzyć się w zestaw kluczy i narzędzi ręcznych, które umożliwią dokręcanie złączek oraz rur. Kluczowe będzie również posiadanie wkrętarki elektrycznej lub akumulatorowej, która przyspieszy proces montażu. Do cięcia rur pneumatycznych przydatna będzie piła do metalu lub specjalne nożyce, które zapewnią czyste i precyzyjne cięcia. Niezbędne będą także złączki i rury odpowiedniego rodzaju, wykonane z materiałów odpornych na wysokie ciśnienie, takich jak stal nierdzewna czy mosiądz. Warto również zaopatrzyć się w uszczelki oraz taśmy teflonowe, które pomogą w zapewnieniu szczelności połączeń. Dodatkowo, manometry oraz zawory bezpieczeństwa są kluczowe dla monitorowania ciśnienia w systemie oraz zapobiegania ewentualnym awariom. Nie można zapomnieć o śrubach i nakrętkach, które będą potrzebne do mocowania elementów konstrukcyjnych.
Jakie są różnice między kompresorami tłokowymi a śrubowymi?
Wybór odpowiedniego typu kompresora do połączenia ma kluczowe znaczenie dla efektywności całego systemu. Kompresory tłokowe działają na zasadzie sprężania powietrza za pomocą ruchomego tłoka, co pozwala na uzyskanie wysokiego ciśnienia w krótkim czasie. Są one zazwyczaj tańsze w zakupie i łatwiejsze w serwisowaniu, co czyni je popularnym wyborem w małych warsztatach i gospodarstwach domowych. Z drugiej strony, kompresory śrubowe charakteryzują się większą wydajnością oraz dłuższą żywotnością, co sprawia, że są bardziej odpowiednie do zastosowań przemysłowych. Działają one na zasadzie sprężania powietrza za pomocą wirujących śrub, co pozwala na ciągłą pracę bez przerw. Kompresory śrubowe są cichsze i bardziej energooszczędne niż ich tłokowe odpowiedniki, co może przynieść znaczne oszczędności w dłuższej perspektywie czasowej. Warto również zauważyć, że kompresory tłokowe mogą generować większe drgania i hałas podczas pracy, co może być istotnym czynnikiem przy wyborze urządzenia do środowiska pracy.
Jakie są najlepsze praktyki przy używaniu połączonych kompresorów?
Aby zapewnić optymalne działanie połączonych kompresorów, warto przestrzegać kilku najlepszych praktyk dotyczących ich użytkowania i konserwacji. Przede wszystkim należy regularnie monitorować ciśnienie robocze w systemie oraz sprawdzać stan wszystkich połączeń i złączek pod kątem ewentualnych nieszczelności. W przypadku wykrycia jakichkolwiek problemów należy niezwłocznie je naprawić, aby uniknąć dalszych uszkodzeń lub obniżenia wydajności systemu. Ważne jest również przeprowadzanie regularnych przeglądów technicznych obu kompresorów oraz ich konserwacja zgodnie z zaleceniami producenta. Należy pamiętać o wymianie oleju oraz filtrów powietrza w ustalonych interwałach czasowych, co pozwoli na utrzymanie urządzeń w dobrym stanie technicznym. Kolejną istotną praktyką jest unikanie przeciążania kompresorów poprzez dostosowywanie ich pracy do rzeczywistych potrzeb aplikacji. Warto również zadbać o odpowiednią wentylację miejsca pracy, aby zapobiec przegrzewaniu się urządzeń podczas intensywnej eksploatacji.
Jakie są koszty związane z łączeniem dwóch kompresorów?
Koszty związane z łączeniem dwóch kompresorów mogą się znacznie różnić w zależności od wielu czynników, takich jak typ urządzeń, materiały użyte do instalacji oraz dodatkowe akcesoria wymagane do prawidłowego działania systemu. Na początku warto uwzględnić koszt zakupu drugiego kompresora; ceny mogą się różnić w zależności od marki i modelu urządzenia. Dodatkowo należy doliczyć koszty materiałów eksploatacyjnych takich jak rury, złączki oraz uszczelki, które będą niezbędne do prawidłowego montażu układu pneumatycznego. Koszt robocizny również może być znaczącym elementem całkowitych wydatków; jeśli zdecydujesz się na zatrudnienie specjalisty do przeprowadzenia instalacji, warto wcześniej uzyskać kilka ofert cenowych od różnych firm serwisowych. Należy także pamiętać o przyszłych kosztach eksploatacyjnych związanych z energią elektryczną zużywaną przez dwa pracujące jednocześnie kompresory oraz kosztami konserwacji i serwisowania urządzeń.
Jakie są alternatywy dla łączenia dwóch kompresorów?
Jeśli łączenie dwóch kompresorów nie jest możliwe lub opłacalne w danym przypadku, istnieje kilka alternatywnych rozwiązań, które mogą zwiększyć wydajność systemu pneumatycznego. Jednym z nich jest zakup jednego większego kompresora o wyższej wydajności i ciśnieniu roboczym; takie rozwiązanie może okazać się bardziej efektywne niż łączenie dwóch mniejszych jednostek. Inną opcją jest inwestycja w sprężarkę bezolejową lub olejową o lepszych parametrach technicznych dostosowanych do specyficznych potrzeb aplikacji. Można także rozważyć zastosowanie akumulatora powietrznego (zbiornika), który gromadzi sprężone powietrze i uwalnia je w razie potrzeby; to rozwiązanie pozwala na stabilizację ciśnienia w systemie oraz zmniejsza obciążenie samych kompresorów.
Jakie są najczęstsze pytania dotyczące łączenia kompresorów?
Wielu użytkowników ma pytania dotyczące łączenia dwóch kompresorów oraz związanych z tym aspektów technicznych i praktycznych. Często pojawia się pytanie o to, czy można łączyć różne typy kompresorów; odpowiedź brzmi: tak, ale należy zwrócić uwagę na ich parametry robocze oraz kompatybilność techniczną. Inni zastanawiają się nad tym, jakie materiały najlepiej nadają się do budowy układu pneumatycznego; zaleca się stosowanie rur stalowych lub mosiężnych ze względu na ich odporność na wysokie ciśnienie. Użytkownicy często pytają również o to, jak często należy przeprowadzać konserwację połączonych kompresorów; eksperci zalecają regularne przeglądy co najmniej raz w roku oraz bieżące monitorowanie stanu technicznego urządzeń podczas ich eksploatacji. Pytania dotyczą także kosztów związanych z takim przedsięwzięciem; warto dokładnie oszacować wszystkie wydatki przed podjęciem decyzji o połączeniu dwóch jednostek.