Destylarka do rozpuszczalników to urządzenie, które wykorzystuje proces destylacji do oddzielania różnych substancji chemicznych na podstawie ich temperatury wrzenia. W praktyce oznacza to, że gdy mieszanina rozpuszczalników jest podgrzewana, substancje o niższej temperaturze wrzenia parują jako pierwsze, a następnie skraplają się w chłodnicy. W ten sposób można uzyskać czystsze frakcje rozpuszczalników, co jest niezwykle istotne w laboratoriach chemicznych oraz w przemyśle. Proces ten wymaga precyzyjnego kontrolowania temperatury oraz ciśnienia, aby zapewnić optymalne warunki dla destylacji. Warto również zauważyć, że różne rodzaje destylarek mogą być używane w zależności od specyfiki zastosowań. Na przykład, destylarki prostokątne są często wykorzystywane do większych ilości substancji, podczas gdy kolumnowe destylarki oferują wyższą efektywność separacji.
Jakie są najważniejsze elementy destylarki do rozpuszczalników
Każda destylarka do rozpuszczalników składa się z kilku kluczowych elementów, które współpracują ze sobą, aby umożliwić skuteczny proces destylacji. Na początku mamy zbiornik na mieszankę, który jest miejscem, gdzie umieszczane są surowce do destylacji. Następnie znajduje się system grzewczy, który podgrzewa mieszaninę do odpowiedniej temperatury. Kolejnym istotnym elementem jest chłodnica, która schładza pary i przekształca je z powrotem w ciecz. Warto również zwrócić uwagę na kolumnę destylacyjną, która może być wyposażona w różne rodzaje wypełnień lub talerzyków, co zwiększa efektywność separacji substancji. Dodatkowo niektóre modele posiadają systemy automatycznej kontroli temperatury oraz ciśnienia, co znacznie ułatwia obsługę urządzenia i zwiększa jego bezpieczeństwo.
Jakie są zastosowania destylarki do rozpuszczalników w różnych branżach
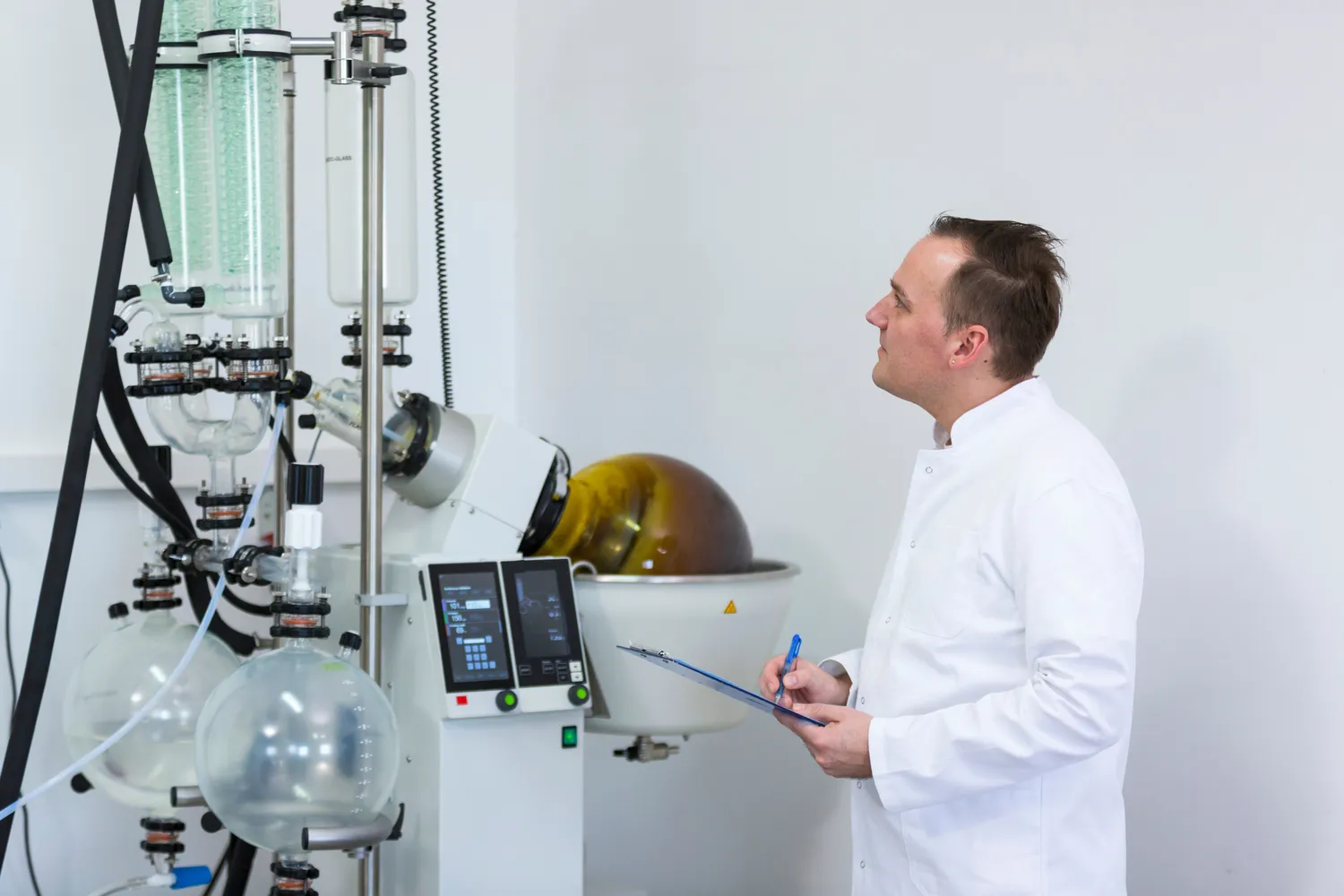
Destylarka do rozpuszczalników znajduje szerokie zastosowanie w wielu branżach przemysłowych oraz naukowych. W laboratoriach chemicznych jest wykorzystywana do oczyszczania substancji chemicznych oraz przygotowywania prób do dalszych badań. Dzięki możliwości separacji różnych frakcji rozpuszczalników można uzyskać czystsze produkty, co ma kluczowe znaczenie dla jakości prowadzonych badań. W przemyśle farmaceutycznym destylarki są używane do produkcji leków oraz substancji czynnych, gdzie czystość składników jest absolutnie niezbędna. Również w branży kosmetycznej destylacja odgrywa ważną rolę przy produkcji olejków eterycznych i innych składników aktywnych. W sektorze petrochemicznym destylarki są stosowane do separacji różnych frakcji ropy naftowej, co pozwala na uzyskanie paliw oraz innych produktów chemicznych.
Jakie są korzyści z używania nowoczesnych destylarek do rozpuszczalników
Nowoczesne destylarki do rozpuszczalników oferują szereg korzyści, które znacząco poprawiają efektywność procesów produkcyjnych oraz laboratoryjnych. Przede wszystkim nowoczesne modele charakteryzują się wyższą wydajnością energetyczną, co przekłada się na mniejsze zużycie energii podczas procesu destylacji. Dodatkowo wiele z nich wyposażonych jest w zaawansowane systemy automatyzacji, które pozwalają na precyzyjne monitorowanie i kontrolowanie parametrów pracy urządzenia. Dzięki temu możliwe jest osiągnięcie lepszej jakości produktu końcowego oraz minimalizacja ryzyka błędów ludzkich. Nowoczesne destylarki często posiadają także funkcje samoczyszczenia oraz łatwego dostępu do komponentów serwisowych, co znacznie ułatwia ich konserwację i naprawy. Co więcej, dzięki zastosowaniu innowacyjnych materiałów odpornych na działanie agresywnych chemikaliów żywotność tych urządzeń jest znacznie dłuższa niż w przypadku starszych modeli.
Jakie są różnice między destylarkami do rozpuszczalników a innymi metodami separacji
Destylarka do rozpuszczalników wyróżnia się na tle innych metod separacji, takich jak ekstrakcja czy filtracja, dzięki swojej specyfice działania oraz zastosowaniom. Proces destylacji opiera się na różnicach w temperaturze wrzenia substancji, co pozwala na ich efektywne oddzielanie. W przeciwieństwie do ekstrakcji, która polega na rozpuszczaniu jednego składnika w innym rozpuszczalniku, destylacja nie wymaga użycia dodatkowych substancji chemicznych. To sprawia, że proces ten jest często bardziej ekologiczny i mniej kosztowny. Dodatkowo, destylacja może być stosowana do oczyszczania substancji o wysokiej czystości, co jest kluczowe w wielu branżach, takich jak farmaceutyka czy chemia analityczna. Filtracja natomiast jest ograniczona do separacji ciał stałych od cieczy i nie jest w stanie oddzielić substancji chemicznych na podstawie ich właściwości fizycznych. Warto również zauważyć, że destylarki mogą być wykorzystywane w sposób ciągły, co zwiększa wydajność procesów przemysłowych.
Jakie są najczęstsze problemy związane z użytkowaniem destylarki do rozpuszczalników
Podczas korzystania z destylarki do rozpuszczalników mogą wystąpić różnorodne problemy, które mogą wpłynąć na efektywność procesu oraz jakość uzyskiwanych produktów. Jednym z najczęstszych problemów jest nieprawidłowe ustawienie temperatury, co może prowadzić do niepełnej separacji substancji lub ich degradacji. Zbyt wysoka temperatura może spowodować przegrzanie i uszkodzenie elementów urządzenia, podczas gdy zbyt niska może skutkować niewystarczającą wydajnością. Innym istotnym zagadnieniem jest kondensacja par, która może być utrudniona przez zanieczyszczenia lub niewłaściwe ustawienia chłodnicy. W takich przypadkach pary mogą nie skraplać się prawidłowo, co prowadzi do strat materiałowych oraz obniżenia jakości produktu końcowego. Ponadto użytkownicy muszą być świadomi ryzyka związanego z pracą z substancjami łatwopalnymi oraz toksycznymi, co wymaga odpowiednich środków ostrożności i zabezpieczeń.
Jakie są koszty zakupu i eksploatacji destylarki do rozpuszczalników
Koszty zakupu oraz eksploatacji destylarki do rozpuszczalników mogą się znacznie różnić w zależności od jej typu, wielkości oraz zastosowań. Na rynku dostępne są zarówno proste modele laboratoryjne, jak i zaawansowane urządzenia przemysłowe, których ceny mogą wynosić od kilku tysięcy złotych do nawet kilkuset tysięcy złotych. Przy wyborze odpowiedniej destylarki warto zwrócić uwagę na jej wydajność oraz możliwości dostosowania do konkretnych potrzeb produkcyjnych. Koszty eksploatacji obejmują m.in. zużycie energii elektrycznej, konserwację oraz ewentualne naprawy. Nowoczesne modele charakteryzują się wyższą efektywnością energetyczną, co może znacząco obniżyć koszty operacyjne w dłuższej perspektywie czasowej. Dodatkowo warto uwzględnić koszty związane z zakupem surowców oraz ich transportem, które również mogą wpływać na całkowity bilans ekonomiczny użytkowania destylarki.
Jakie są najlepsze praktyki dotyczące obsługi destylarki do rozpuszczalników
Aby zapewnić prawidłowe działanie destylarki do rozpuszczalników oraz maksymalizować jej wydajność, istotne jest przestrzeganie najlepszych praktyk dotyczących jej obsługi. Przede wszystkim należy dokładnie zapoznać się z instrukcją obsługi dostarczoną przez producenta i stosować się do zaleceń dotyczących ustawień temperatury oraz ciśnienia. Regularne kontrole stanu technicznego urządzenia są kluczowe dla uniknięcia awarii oraz zapewnienia bezpieczeństwa pracy. Użytkownicy powinni również dbać o czystość zbiornika oraz chłodnicy, aby uniknąć zanieczyszczeń wpływających na jakość uzyskiwanych produktów. Ważne jest także stosowanie odpowiednich środków ochrony osobistej podczas pracy z substancjami chemicznymi oraz przestrzeganie zasad BHP. W przypadku wystąpienia jakichkolwiek nieprawidłowości należy natychmiast przerwać pracę urządzenia i przeprowadzić diagnostykę problemu.
Jakie są przyszłe trendy w technologii destylacji rozpuszczalników
Przemysłowy rozwój technologii destylacji rozpuszczalników zmierza ku coraz większej automatyzacji oraz wykorzystaniu nowoczesnych materiałów i technologii. W przyszłości możemy spodziewać się dalszego wzrostu efektywności energetycznej urządzeń dzięki zastosowaniu innowacyjnych systemów grzewczych oraz chłodzących. Również rozwój technologii cyfrowych umożliwi lepsze monitorowanie procesów destylacyjnych poprzez zastosowanie sensorów i systemów analitycznych, co pozwoli na optymalizację parametrów pracy w czasie rzeczywistym. W kontekście ochrony środowiska rośnie zainteresowanie ekologicznymi metodami separacji, które minimalizują zużycie energii oraz generowanie odpadów chemicznych. Możliwe jest także wdrażanie nowych materiałów odpornych na działanie agresywnych substancji chemicznych, co zwiększy trwałość i niezawodność urządzeń.
Jakie są różnice w destylacji prostej i frakcyjnej w kontekście rozpuszczalników
W kontekście destylacji rozpuszczalników istotne jest zrozumienie różnic między destylacją prostą a frakcyjną, ponieważ każda z tych metod ma swoje specyficzne zastosowania oraz zalety. Destylacja prosta jest najczęściej stosowana do separacji substancji, które mają znacznie różniące się temperatury wrzenia. Proces ten polega na podgrzewaniu mieszaniny, aż jedna z substancji zacznie parować, a następnie skraplaniu pary. Jest to metoda stosunkowo szybka i łatwa, jednak jej efektywność maleje w przypadku substancji o zbliżonych temperaturach wrzenia. W takich sytuacjach lepszym rozwiązaniem jest destylacja frakcyjna, która wykorzystuje kolumnę destylacyjną wyposażoną w talerzyki lub wypełnienia, co pozwala na wielokrotne skraplanie i parowanie substancji. Dzięki temu możliwe jest uzyskanie wyższej czystości frakcji oraz skuteczniejsze oddzielanie składników o podobnych temperaturach wrzenia.